[ad_1]
The selection of duct system materials determines the success or failure of a project because it directly affects the structure. The general distinctions between polyvinyl chloride (PVC) and chlorinated polyvinyl chloride (CPVC) are familiar to most plumbers, yet ductwork applications require additional evaluation.
The performance of PVC and CPVC ducts under various conditions requires knowledge from plumbers who work with HVAC technicians or manage complete retrofit jobs to achieve safe, efficient, and code-compliant systems.
The article examines the essential technical distinctions between PVC and CPVC duct systems, focusing on aspects most relevant to field plumbers, including temperature resistance, chemical compatibility, ease of installation, and regulatory requirements.
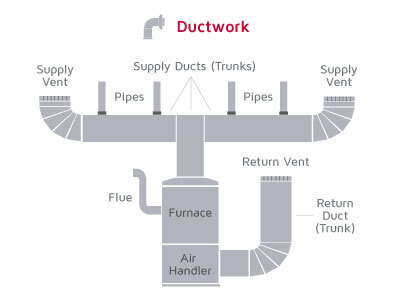
Duct Systems Specifically: Why It’s a Different Ball Game
Ductwork isn’t just piping. The primary purpose of pipes is to transport water and waste, but ducts serve to distribute air and, occasionally, toxic fumes or hot exhaust. The design requirements for ductwork, including pressure and materials, differ significantly from those of standard plumbing applications.
According to Lennox, ductwork is “a system of channels used to distribute air throughout a building.” The work of plumbers requires them to handle components that need to be both lightweight and corrosion-resistant, particularly when working with exhaust in mechanical rooms and fume extraction in laboratories or industrial settings. Your responsibility will include duct connection and material maintenance throughout their entire operational period, even though you will not be responsible for constructing the whole HVAC system.
Fundamental Differences: What You Probably Already Know and What You Need to Know
Let’s get the basics out of the way. Most plumbers already know this, but here’s a refresher in the context of ductwork:
- Temperature Tolerance: PVC is rated up to 140°F, while CPVC can handle up to 200°F. If you’re dealing with warm exhaust or chemical fumes, that extra 60 degrees can be a dealbreaker.
- Chemical Resistance: Both are good, but CPVC outperforms PVC in terms of resistance to acids, bases, and corrosive gases.
- Strength & Sizing: Both come in standard duct sizes, but CPVC tends to be more rigid and stable under stress.
- Cost: CPVC is generally 25–40% more expensive than PVC. However, when a failure could result in system-wide contamination or code violations, it can pay off in the long run.
The process becomes difficult because plumbing and mechanical codes do not match. The International Residential Code (IRC) permits PVC ducts, but the Uniform Mechanical Code (UMC) bans their use in commercial buildings. CPVC passes both flame and chemical tests because of its superior ratings.
The legal status of building materials varies across different areas, so check local regulations at the city, county, and state levels. NSF 61, ASTM F441, and UL 94 V-0 ratings should be checked.
CPVC meets higher standards of fire and chemical safety, which makes it a safer choice for many duct applications. It also meets inspector requirements more effectively in high-risk or regulated environments, such as hospitals or laboratories, particularly when there is uncertainty.
Compatibility and Installation Considerations
Plumbers often overlook material compatibility checks, particularly when working with PVC or CPVC ducts that need to be connected to metals, or when using untested gaskets or sealants.
The connection of galvanized steel components to CPVC ducts through direct contact without an isolating gasket may lead to galvanic corrosion. The installation requires connectors and sealants, which are specifically designed for CPVC applications.
PVC cement does not function properly with CPVC materials. The solvent used for CPVC requires stronger properties and slower curing time.
Plumbers perform PVC cutting operations and gluing tasks. The installation process for CPVC follows the same steps as PVC but requires additional procedures:
- CPVC requires an extended curing period, which becomes more significant during cold weather conditions, thus affecting project schedules.
- The cutting process for both materials remains straightforward but CPVC requires more precise and cleaner cuts because it breaks easily.
- The use of fine-tooth blades, combined with support cuts, will prevent CPVC from cracking during the cutting process.
- Metal saw blades should be used with caution when working with plastics
In long duct runs, expansion and contraction can cause buckling or cracking.
- PVC expands about 3x more than CPVC over the same temperature rise.
- If you’re working in a facility with frequent temperature swings, CPVC offers better dimensional stability and less maintenance down the line.
CPVC generally earns higher marks for flame and smoke resistance. It typically meets UL 94 V-0 standards, which means it self-extinguishes quickly and produces less toxic smoke in a fire scenario.
This is especially important in:
- Healthcare facilities
- Schools
- Commercial kitchens
- Anywhere with life-safety code requirements
PVC, on the other hand, can produce thick black smoke and continues to burn once ignited.
While ductwork doesn’t usually carry fluid pressure, static pressure still matters—especially in exhaust or fume systems.
- PVC ductwork typically handles lower pressure (up to 10 inches of water column).
- CPVC ducts can manage slightly higher pressures, and with better rigidity, they resist collapse under vacuum.
For high-performance fume extraction or long vertical runs, CPVC has the edge.
Conclusion: When to Use Which?
Here’s the bottom line:
Scenario | Recommended Material |
Low-temp air movement | PVC duct |
Chemical fume exhaust | CPVC duct |
High-temp or steam ventilation | CPVC duct |
Tight budget, low risk | PVC duct |
Hospitals, labs, or code-heavy installations | CPCV duct |
Jurisdictional uncertainty | CPVC duct |
Plumbers who perform HVAC installations or manage crossover systems should understand the distinction between PVC and CPVC ducts, as it represents essential knowledge for proper job execution. Knowledge of performance boundaries, installation characteristics, and regulatory standards for each material helps prevent both expensive callbacks and inspection failures, as well as system breakdowns in the future.
Your knowledge enables you to select appropriate ductwork with confidence while improving your collaboration with HVAC technicians and maintaining system integrity through all joints, runs, and transitions under both physical and actual pressure.
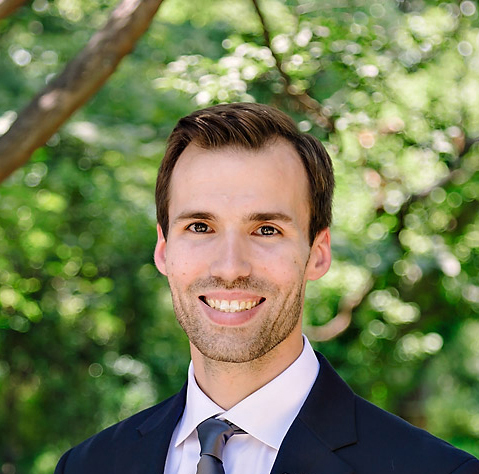
Author Bio: Mark Ligon is the marketing manager at Commercial Industrial Supply, a supplier of commercial & industrial piping, fittings, valves, filtration products, and accessories. Ligon enjoys educating businesses on the specific parts of piping systems so managers can make informed decisions.
[ad_2]
Source link